「炭素質・黒鉛質の違い」のページでは、焼成温度の違いによる特性を紹介いたしました。「黒鉛の製造方法」では、弊社のメインの取扱い材料である黒鉛グラファイトのブロックの製造方法を紹介致します。
粉砕(Pulverizing)
黒鉛グラファイトの原料「ピッチコークス」「ニードルコークス」「コールタールピッチ」を粉砕します。カーボンの原料は、粒子の細かさも材料の特性に関係するため、数種類の粒度のカーボン粉が準備されます。
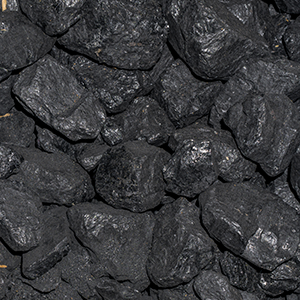
分別(Dividing)
粉砕したコークスを粒子の大きさに振り分けます。また、コークスは、産地(国)により特性が多少違います。振り分けたコークスは、それぞれの産地・粒度で管理・保管されます。
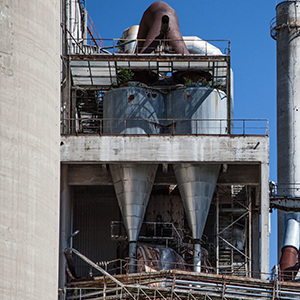
配合(Mixing)
黒鉛グラファイトの材料の品種別に、粒子の大きさや産地の違いの複数のコークスを混ぜ合わせます。グラファイトの素材メーカーでは、数種~十数種の材料のラインナップがあります。 それぞれの材料の特性に合わせた配合が施されてています。
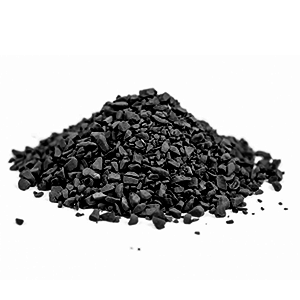
混練・捏合(Kneading)
配合したコークスと、コールタールピッチを混ぜ合わせます。コールタールは液体でバインダーの役割をします。また焼成を行うと、コールタールピッチも炭化して、グラファイトの原料になります。
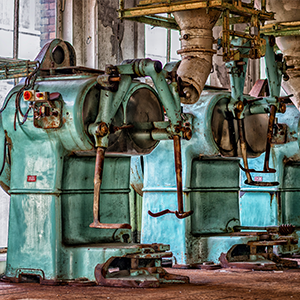
成形(Forming)
混練・捏合した原料を成形します。成形の方法は以下の種類になります。成形方法により材料の特性に違いがあります。
押出成形(Extrusion molding)
押出成形は、プレス機の片側に押さえが無く、一方向より材料を押し出して成形する製法です。材料に掛かる圧力は、材料が抜けていく方向と、形状を整えるダイスを材料が抜ける時に受ける圧力になります。 その為、素材に方向性が出来ます。方向性とは、電流の流れやすい方向や、材料の曲げ強さなどの強度に向きが発生する事をいいます。
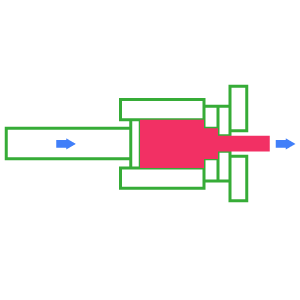
型押成形(Mold extrusion)
プレス機を使い、上(もしくは上下方向)より圧力を掛けて材料を成形する方法です 材料に掛かる圧力が上下方向になりますので、押出成形と同様に材料に方向性が出来ます。また、材料の外周部分と内側には、材料の歪みも発生しております。その為、材料を切り出す位置でも強度など多少の差異があります。
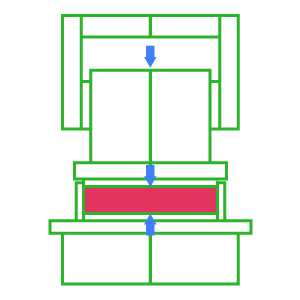
冷間静水圧プレス成形(Cold isostatic pressing)
冷間静水圧プレス成形は、英文を訳してCIP成形とよく言われています。ゴム型に封入されたカーボン原料を封入します。封入した材料を、水溶液に投入して水圧を材料へ掛けます。 ゴム型に入れるプレス方法なので、CIP成形の事を「ラバープレス法」とも言われます。また、水溶液中で材料へ圧力を掛けると、全方向から圧力が掛かるため、プレスされた材料に方向性が出来ません。 言えば均一な材料となります。その為、CIP材の事を「等方性黒鉛」とも言われます。CIP材は押出材と比較すると、おおよそ曲げ強さが約2倍、引張り強さも約2倍にあります。
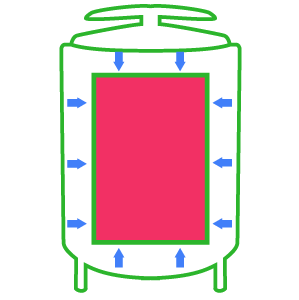
振動成形(Vibration molding)
振動成形は、カーボンの原料を型に入れ、型に振動を与えることにより、材料の空隙を少なくした材料です。振動成型を用いる事が多い、ゴム材料や樹脂材料は、振動作業の後にプレスの工程が通常入ります。カーボンの原料は、焼成後に含浸処理を行われることから、プレス成型をせずに焼成されるカーボン材料もあります。装置が簡素化され、作業時間も短くなることから、材料が比較的安くなるメリットがあります。原料の粒子の大きさを小さくすると、見た目はCIP材に近くなり、見た目では判断できないほどの材料を作ることが出来ます。 プレスの工程が入っていない材料の場合は、材料の強度が弱くなります。
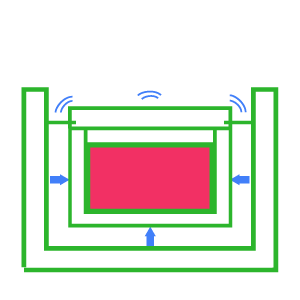
焼成(Baking)
プレスしたカーボン材料は、コークスの粉末とバインダーのコールタールが混じっており形を保つ事ができます。 その材料を、炉に入れ約1000度位で焼きます。一回目の焼成を「一次焼成」と言います。一次焼成により、バインダー分の一部は気化し、一部は炭化して原料に変化します。1,000度くらいでの焼成ですので、カーボン原料はまだ炭素質です。
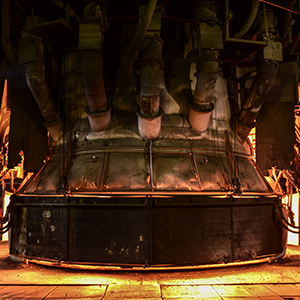
ピッチ含浸(Impregnation)
一次焼成で気化したコールタールピッチの部分は、空隙が出来ています。空隙を塞いで材料の密度を上げる為に、もう一度、コールタールピッチに材料を漬け込みます。ピッチ含浸をしたカーボンを、再度焼成します。この作業は1~2度繰り返し施されます。 2回目の焼成を二次焼成。3回目の焼成を三次焼成といいます。
黒鉛化(Graphitizing)
カーボン原料の空隙が無くなった所で、高温2,300度以上の温度を材料に掛けます。この作業は約1ヶ月ほど行います。高温度処理により、コークス中のカーボン原子がグラフェン構造に発達をします。これにより、カーボンは黒鉛グラファイトになります。
外面加工および機械加工(Machining)
黒鉛化された材料の表面は「黒皮」と呼ばれる、一層硬い層が出来ています。また表面はデコボコしており、平面が出来ていません。そこで20~30mmの厚みで材料の外面を切断し「黒皮」を除去します。黒皮の除去をした後、製品の加工を行います。
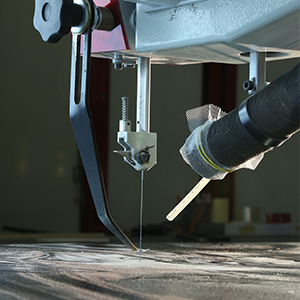
高純度処理(Purification)
黒鉛内の不純物(灰分)に塩素ガスなどのハロゲンガスを吹きつけ、黒鉛グラファイトの純度を上げます。 高純度処理には「高純度処理(8~10ppm)」と「超高純度処理(2~3ppm)」がございます。通常、弊社の様なカーボンの加工会社では、材料は空気にさらされているため、20ppm程度には純度が落ちている事が考えられます。 弊社では、お客様に「製品純化を行っていない製品については、純度が落ちています」とお伝えし、承認を得て製品を納めさせていただいております。 純度が必要な場合は加工後に、製品純化を行います。
特殊処理(Special Treatment)
製品の用途に応じ、SiCコートや、ガラス状カーボンコート、溶射処理などの処理を施します。
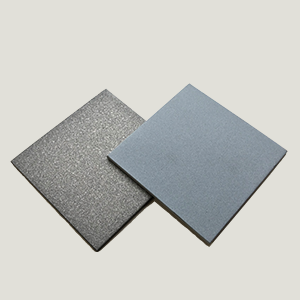
検査・出荷(Inspection and Shipping)
出来上がった製品の品質検査を行い、出荷されます。
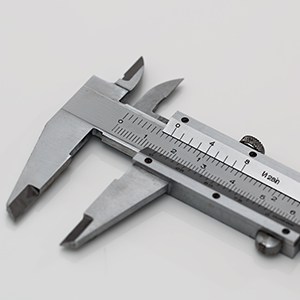
「黒鉛の製造方法」ではグラファイトの素材の製造方法を紹介いたしました。
カーボンは身の回りの生活用品などの原料や装置部品として色々なところで使われています。次の「身近なカーボン製品」身近な黒鉛製品を紹介致します。